A new 2D auxetic material
- Zian Jia
- Feb 15, 2019
- 2 min read
Updated: Mar 14, 2019
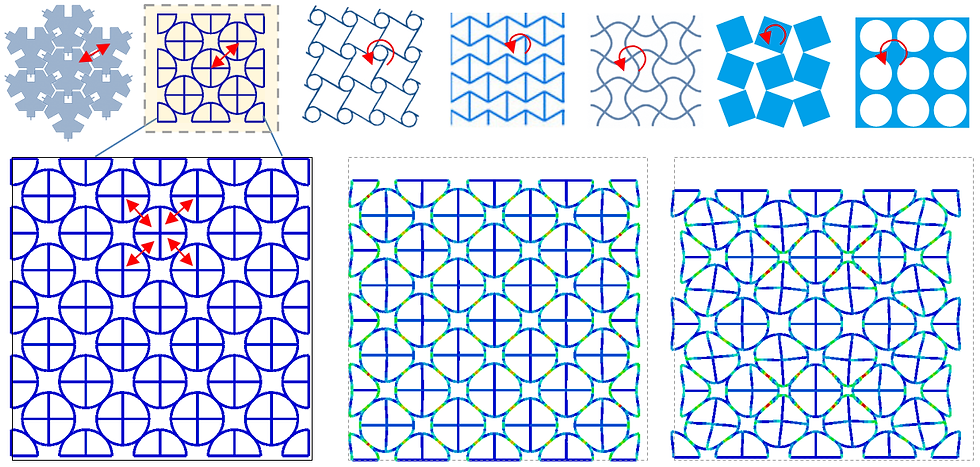
In this post, I'll show a 2D auxetic material design approach that's based on the indent of contacted structural element, which is different from most of the currently available auxetic materials (rotation based). Each structural element is a cylinder with a cross reinforcement. The cross reinforcement is essential because cylinders will bulge under compression as demonstrated in the following figure. Note that the proposed structural material is four-fold symmetric (not isotropic), therefore, the Poisson's ratio can be greater than 0.5. As an example, the material shown in the following figure exhibits a Poisson’s ratio of 0.66.

Since the proposed material uses a "indent" mechanism, analogy to that of sleeved slider units and different from most current available auxetic material (rotation based), thereby, novel applications are made possible. In the following, I'll discuss several directions that we can further work on.
1. 2D isotropic auxetic material
By arranging the structural elements in a hexagonal pattern, we can design a 2D isotropic auxetic material. Note that a 2D material with hexagonal symmetry is isotropic. The material properties can be further tuned by changing the geometric parameters.
2. Harnessing snap-through instability
Because the auxetic material is based on element indentation, snap through instability can be achieved with a proper selection of the geometric parameters. When snap through takes place, negative incremental stiffness may appear, which can be further used to improve the material's energy absorption and energy dissipation. One design to magnify the effect of snap through instability is also shown below.
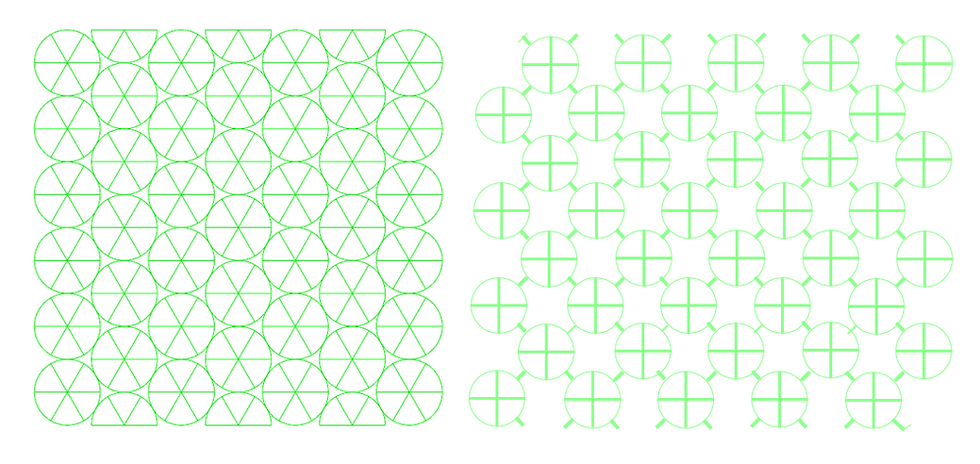
3. Programmable/active controllable materials
By engaging the structural elements similar to a gear system,we can rotate the whole material system using one controlling parameter - the angle of rotation. That is, in a engaged system, when we rotate one elements, all the rest elements will rotate correspondingly.
Furthermore, when the structural elements are rotated, the stiffness and Poisson's ratio of the material will change between a compliant state (negative Poisson's ratio) and a stiff state (positive Poisson's ratio) as demonstrated in the figure.
Based on these two features, we can achieve programmable material properties including stiffness and Poisson's ratio by only varying one parameter, i.e., the angle of rotation. Moreover, when using multiple inputs to control multiple layers of the structural material, more material functions can be achieved with actively controlled.
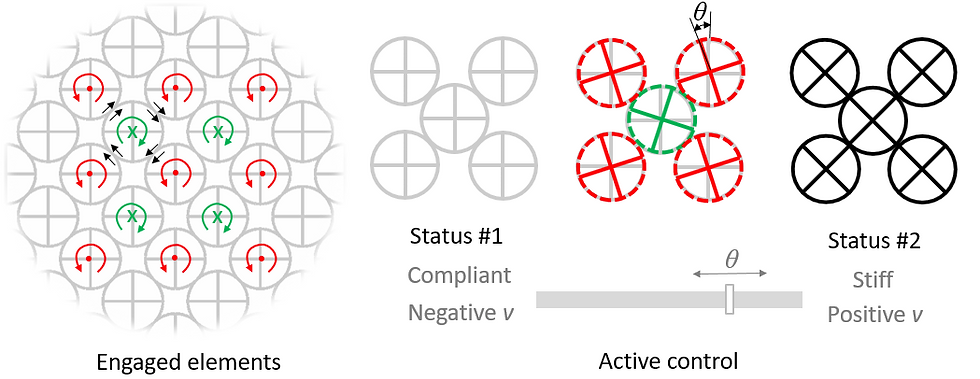
4. 3D multi-negative materials
For 3D spherical shell elements, we do not need the cross reinforcements to obtain the "indentation" effect. Thereby, it's actually more simple in 3D. We've finished one manuscript on the 3D auxetic material, discussion can be found in [post]. And we're trying to reveal more functions of the 3D hollow sphere foam material.
5. Potential for haptic applications
By further sealing the cylinder and pump pressured air into the cylindrical shell, we can adjust the stiffness of the material with a larger range. The material concepts presented here provide new approaches to design haptic materials. Applications of haptic gloves are already available in companies like HaptX. Attached is a YouTube video explaining the HaptX gloves.
Commentaires