Structural materials
The production of stronger, tougher, and smarter materials is transferring from the discovery of new bulk material toward the rational design of material architecture, known as the structural materials or architected materials. We use biological materials as systems to investigate the structure, properties, and design of structural materials. The learned knowledge are examined by fabricating and testing bioinspired structural materials.
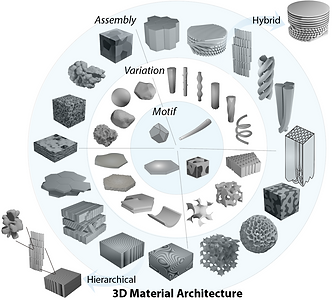
Biological materials
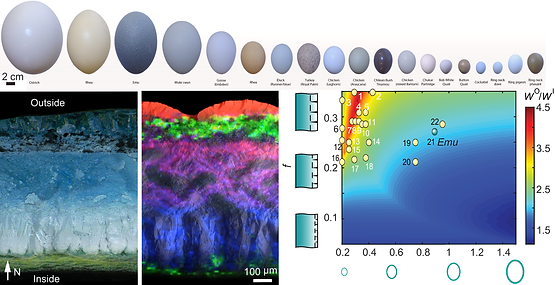
• Eggshells
Eggshell stands apart from other biocomposites like seashells, enamel, and bone in many aspects. It is fast-forming (formed within 24h), short-lived (lasting only a few weeks or months), highly dynamic (the developing chick sequesters calcium from the shell to support bone growth), and most impressively, tough (to external load) but easily breakable (to inner load). We have uncovered many unique design principles of eggshells and found their engineering applications.
• Mechanics of eggshells (thin brittle shells with microstructure)
Theoretical studies on thin shells have a long history, attracting the attention of many famous mechanists (Koiter 1967; Timoshenko and Woinowsky-Krieger 1959; Von Karman and Tsien 1939; Love 2013 ), which has helped to develop theoretical frameworks to predict the stiffness (Reissner 1946; Updike 1972; Vella 2011), deformation (Jenkins and Leonard 1991; Leonetti 2019), and buckling (Hutchinson 2016; Koiter 1970) of shell structures. Most of these studies focus on homogeneous shells that can undergo large deformation, our knowledge on the fracture of brittle shells with specialized heterogeneity and microstructure is still limited. We combine systematic chemical-microstructural characterization, mechanical testing, artificial eggshell fabrication, and theoretical modeling to study the mechanics of eggshells and thin, brittle shells in general.


_tif.png)
• Cuttlebone
Cuttlefish are marine mollusks with an ultra-lightweight cuttlebone, which is highly mineralized (>95%) and used for buoyancy. Impressively, cuttlebone is highly damage-tolerant and can withstand strong water pressure. We use analytical methods, including synchrotron-based micro-CT, in-situ mechanical tests, DIC, and FEA to examine the microstructure and multiscale mechanics of the cuttlebone.
The chambered microstructure of the cuttlebone achieves high specific stiffness and high energy absorption because of an optimal waviness gradient. The wavy and corrugated walls are nearly as stiff as straight walls but restrict maximum stress to well-defined locations. Biologically inspired cellular ceramics have potential applications in packing, transportation, and infrastructure.
-
Z. Jia, Z. Deng, and L. Li, Mineralized biological materials as model systems for structural composites: 3D architecture. Invited review paper, Advanced Materials. 2106259 (2022). [pdf]
-
Z. Deng, Z. Jia, and L. Li, Mineralized biological materials as model systems for structural composites: intrinsic properties. Invited review paper, Advanced Sciences. in press (2022).
-
T. Yang^, H. Chen^, Z. Jia, Z. Deng, L. Chen, E. Peterman, J. Weaver and L. Li, A damage-tolerant, dual-scale, single-crystalline microlattice in the knobby starfish, Protoreaster nodosus. Science, 375, 647 (2022). [pdf] [Cover]
-
M. C. Stoddard, Z. Deng, Z. Jia, S. Amini, E. M. Peterman, A. Masic, J. C. Weaver, and L. Li, Strong but breakable: biomechanical design of the emu eggshell. in submission (2022). [Video]
-
Z. Jia, Z. Deng, L. Kadlec, M. C. Stoddard and L. Li, Mechanics of a tough and easily breakable structure in biology: defect and soft membrane engineering in eggshells. (2022). in submission. [manuscript]
-
T. Yang^, Z. Jia^, H. Chen, Z. Deng, W. Liu, L. Chen and L. Li, Mechanical design of the highly porous cuttlebone: A bioceramic hard buoyancy tank for cuttlefish. PNAS 117, 38 (2020): 23450-23459. [pdf] [vt news] [phys.org]

Bioinspired structural materials
-
Microstructure for tailored properties.
By studying the microstructure of biomaterials, we have 3D printed architected materials with tailored property combinations of flexibility/stiffness, strength, toughness, energy dissipation, and fast response. The design principle is using material architecture to control the deformation field, crack location, and crack pattern. The performance characters of different structural elements and the optimal integration of these structural elements are also investigated.
-
Z. Jia, Y. Yu, S. Hou, and L. Wang. Biomimetic architected materials with improved dynamic performance. Journal of the Mechanics and Physics of Solids 125 178-197 (2019). [pdf]
-
Z. Jia and L. Wang. 3D printing of biomimetic composites with improved fracture toughness. Acta Materialia,173: 61-73 (2019). [pdf]

• Breaking the performance tradeoffs.
In bulk materials, some properties are correlated and difficult to be improved together, notoriously known as the material performance tradeoffs. By learning from nature, we produced architected composites that break the performance tradeoffs between strength and toughness, flexibility and strength, stiffness and dissipation, and fast response and flexibility.
-
Z. Jia, Y. Yu, and L. Wang, Learning from nature: using material architecture to break dynamic performance tradeoffs. Materials & Design 107650 (2019). [pdf]
-
Y. Chen, Z. Jia, and L. Wang, Hierarchical honeycomb lattice metamaterials with improved thermal resistance and mechanical properties, Composite Structures 152, 395-402 (2016). [pdf]
• Architected surfaces. The concept of architected material is extended to architected surfaces. Our experiment shows that surface architecture design of a beam's surface (10% of the total thickness) is capable to improve the specimen's impact resistance by 64%. [post]

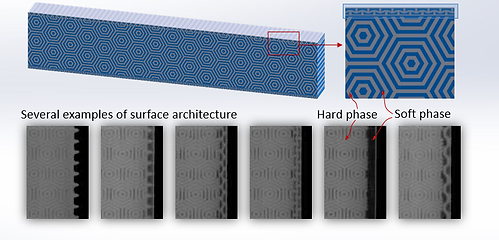
• Hierarchical design. Honeycombs with different second level hierarchical microstructures are investigated, revealing that different hierarchy at different levels is essential to improve a material's stiffness and strength simutaneously. Moreover, we also show the improvement of thermal conductivity and mechanical robustness using structural hierarchy.
Mechanics & metamaterials
The fundamental process of the design, fabrication (or growth), and functionalization of structural materials often involve multiple physical phenomena. This is the motivation for us to study multiphysics mechanisms, often of multiple length scales. Some topics include multifunctional materials, metamaterials, energy materials, and fabrication process modeling.

• Beetle cuticle exhibits vivid coloration for signaling and camouflage, possess micropores for sensing and moisture/chemical transport, while in the meantime it needs mechanical strength and toughness for protection. We reveal that in the flower beetle, its multifunctionality is related to a micro-pillar reinforced nano-multilayer structure. Impressively, the synergy between mechanical and optical properties enable an unique Mechanical-optical damage tolerance.
• Chemical-mechanical coupling in Si-anode
Silicon (Si) is of great interest in the development of high-capacity lithium batteries since it provides over 10 times higher specific capacity than traditional carbon anodes. However, the large volume change of Si (300%~400%) upon the insertion and extraction of lithium generates significant stress that may fracture the Si particles, which ultimately leads to poor cyclability of the Si anode and thus the lithium battery. In collaboration with Prof. Anhua Liu at Xiameng University, we design buffering microstructures to solve this critical issue for reliable deployment of Si anodes.
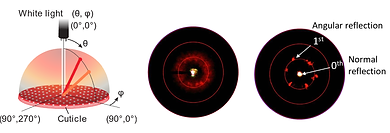

• Hollow sphere foams (HSF) are of great interest in nanofabrication, self-assembly, and drug delivery. It is also a nice structure for lightweight, thermal resistant, triple negative indices, and complete band gap engineering. We develop theoretical models to estimate the mechanic anisotropy and effective thermal conductivity of HSF, which enable designing HSF with porous shells, multi-layered shells, and interfacial thermal resistance down to the nanoscale.

-
Z. Jia, M. Fernandes, Z. Deng, T. Yang, Q. Zhang, A. Lethbridge, J. Yin, J. Lee, L. Han, J. Weaver, K. Bertoldi, J. Aizenberg, M. Kolle, P. Vukusic and L. Li, Microstructural design to achieve mechanical-optical multifunctionality in the cuticle of flower beetle Torynorrhina flammea. PNAS, 118, 25 (2021). [pdf]
-
Z. Jia, F. Liu, X. Jiang and L. Wang, Engineering lattice metamaterials for extreme property, programmability, and multifunctionality. Journal of Applied Physics 127, 15 (2020):150901. [pdf]

• A triple negative metamaterial. Two contacted spheres present snap-through instability. Harnessing the snap-through instability, we developed a 3D mechanical metamaterial with negative stiffness, negative bulk modulus, and negative Poisson’s ratio. Interestingly, both incremental stiffness and incremental Poisson’s ratio approach negative infinity when snap-back occurs, given that the metamaterial is loaded with displacement control. [post]
• Negative incremental stiffness in traditional materials is often referred to as softening, which causes the formation of localized deformation bands and ultimately leads to failure. By contrast, in a double negative metamaterial with Einc < 0 and vinc < -1, the strong ellipticity condition is satisfied, thus the deformation band will be delocalized, preventing premature failure.
-
Z. Jia, Z. Wang, D. Hwang, and L. Wang. Prediction of the effective thermal conductivity of hollow sphere foams. ACS Applied Energy Materials 1(3) 1146-1157 (2018). [pdf]
-
Z. Wang, Z. Jia, L. Wang, B. K. Park, W. Lee, and D. Hwang, Laser-assisted fabrication of thermally insulating syntactic foam, submitted (2019).
-
Z. Jia and L. Wang, 3D metamaterials with stiffness and Poisson's ratio approaching negative infinity, arXiv:1903.00523 (2019). [pdf]
• Auxetic materials. Compared to the rotation based reentrant/chiral lattices and rigid rotating squares, the proposed design is lightweight and possesses better stiffness per mass. The material concept can be further designed to harness the snap-through instability and achieve programmable stiffness, promising for energy absorbing devices and haptic applications. [post]

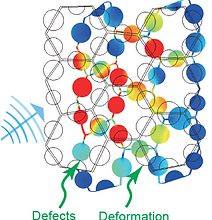

• Phononic crystals with wide and robust band gaps.
Band gaps produced by Bragg scattering can be wide, but are intrinsically sensitive to imperfections and deformations, while band gaps produced by local resonances are robust but typically narrow. By combining these two mechanisms (with the latter dominating), we achieve phononic crystals with simultaneously large and robust band gaps. We show that the suppression of instability is essential for robustness against deformation. Uncertainty analysis further quantifies the effect of imperfection.
-
Z. Jia, Y. Chen, H. Yang, and L. Wang, Designing phononic crystals with wide and robust band gaps, Physical Review Applied 9, 044021 (2018). [pdf]
Engineering & manufacturing

• Overcoming low temperature induced brittleness.
We show that fiber reinforced polymer becomes stiffer, stronger and tougher at lower temperatures, even though the polymer matrix itself becomes brittle at lower temperatures. The underlying mechanism is revealed as the failure mode transition, including micro-buckling, fiber kinking, fiber breakage, and fiber pull-out. The experiment result is verified by theoretical models and numerical simulations. [post1] [post2]
-
Z. Jia, T. Li, F. Chiang, and L. Wang, An experimental investigation of the temperature effect on the mechanics of carbon fiber reinforced polymers, Composites Science and Technology 154, 53-63 (2018). [pdf]

• By using 3D printing to control the interfacial shape at a larger length scale and using the print direction to control the micro-asperity of the interface, we generate bi-material interfaces with hierarchy. Properly designed interfaces are found to improve the fracture toughness/energy absorption effectively, under both static loading and dynamic loading. The introduction of weak interfaces in a relatively brittle material induces cracks to initiate and propagate along prescribed paths, thereby, avoids catastrophic damage. How to optimally design defects/interfaces to make materials stronger and tougher is still under investigation. [video]
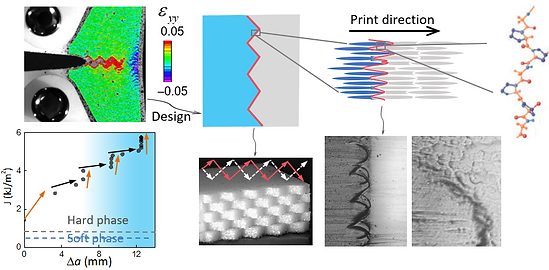

At present, producing structural materials relies mainly on 3D printing, which is often expensive and difficult to mass production. We seek to i) integrate autonomous mechanisms and sustainable compositions for the fabrication of structural materials; ii) improve additive manufacturing techniques by learning from the growth of biological materials; iii) re-innovate traditional fabrication methods for low-cost, mass-producible ways to manufacture functional structural materials.
For instance, by integrating 3D printing, casting, imprinting, traditional pottery, and self-assembling principles, we are able to fabricate artificial eggshells with intricate microstructures and hollow ceramic lattices.
-
Z. Jia and L. Wang. 3D printing of biomimetic composites with improved fracture toughness. Acta Materialia,173: 61-73 (2019). [pdf]