Using surface architecture to improve impact resistance
- Zian Jia
- Mar 14, 2019
- 2 min read
Updated: Mar 23, 2019
Solids are covered by surfaces, which act as interfaces of the bulk material to the surrounding environment. Engineering of material surface has a long history. Back in the middle of the Iron Age, quenching (rapid cooling of a workpiece in water or oil) was used to make swords and axes stiffer and more durable. Nowadays, surface engineering is a thousands of billions market. Add coatings to make a material robust from wear and corrosion is now an engineering standard in industry. In recent decades, new directions of surface science have been proposed, including the super hydrophobic surfaces, optical structural surfaces, meta-surfaces, and multi-functional biological surfaces, just to name a few.
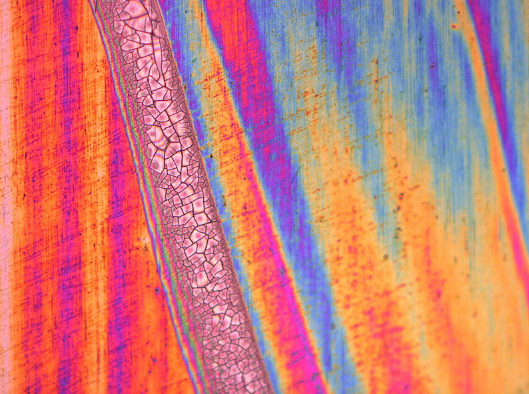
While surface science develops rapidly realizing new physics and functions, engineering surfaces to improve mechanical performance is still limited to traditional topics of surface roughness, surface hardness, and surface wear resistance. This is probably due to the conjecture that surface is relatively thin and thus have a relative small influence on the material's overall performances like stiffness, strength, and toughness. Mathematically, it is possible that a subtle change in surface structure may make a huge difference in the overall performance of the material, especially when nonlinear effects are taken into consideration. Recent researches have shown that material architecture design can push the material property space far beyond that of single phase materials. So, can a similar concept be adopted to design architected surfaces that improve a material's property (impact resistance) significantly?
A subtle change could make a huge difference!
In this post, we demonstrate the effect of surface architecture on a material’s overall impact resistance. Specifically, the concentric hexagonal structural material inspired by bone osteon is selected as the controlled material. 10% of the material’s thickness is replaced with different surface architectures as shown in the following figure.
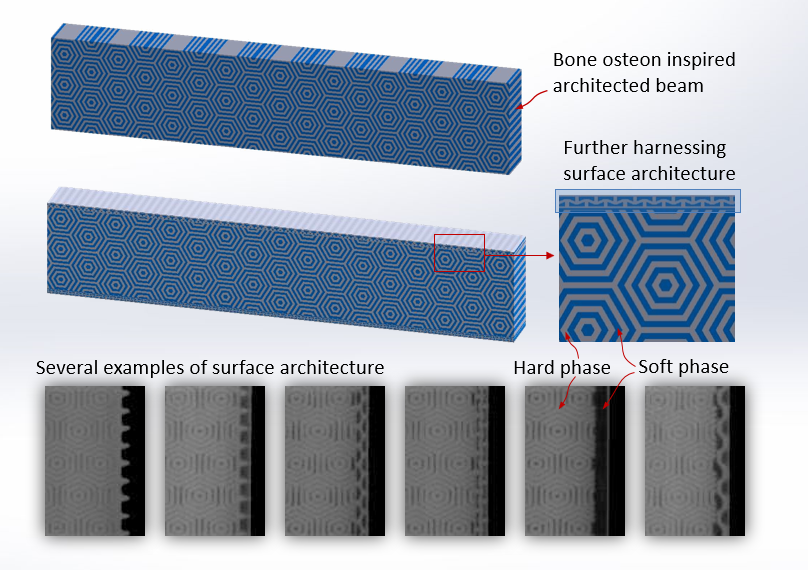
We've designed various types of surface architectures, a few are shown in the above picture. The controlled specimen and the designed specimens are tested under dynamic three point bending conditions using a split- Hopkinson bar system. A comparison of velocity histories is shown in the following figure. The energy absorption of the original specimen is 3.21 J, by contrast, energy absorption of the specimen with architected surface is 5.31 J, achieving an improvement of 64%.

The maximum improvement of energy absorption achieved so far is quite significant. Note that this is only a preliminary experimental result demonstrating how properly designed surface architecture can improve a material's dynamic performance quite significantly. Based on the experimental results, we see at least two potential mechanisms affecting the material's impact resistance: 1) the buffer effect provided by a relatively soft surface layer, for brittle materials, it may significant reduce the stress level right after contact and 2) surface architecture changes the stress distribution on the surface, which promotes progressive cracking and prevents catastrophic damage. A more in-depth understanding of the mechanism requires FEM simulations and nonlinear dynamics analysis, which are works yet to be performed.
Comentarios