Temperature effect on the mechanics of fiber reinforced polymers
- Zian Jia
- Jan 1, 2019
- 2 min read
Updated: Mar 15, 2019
Temperature change may happen in a relatively short time and has significant influence on the materials' mechanical performances. For example, the well-known shipwreck of Titanic is caused by the ductile-brittle transition of steel at a frigid temperature.
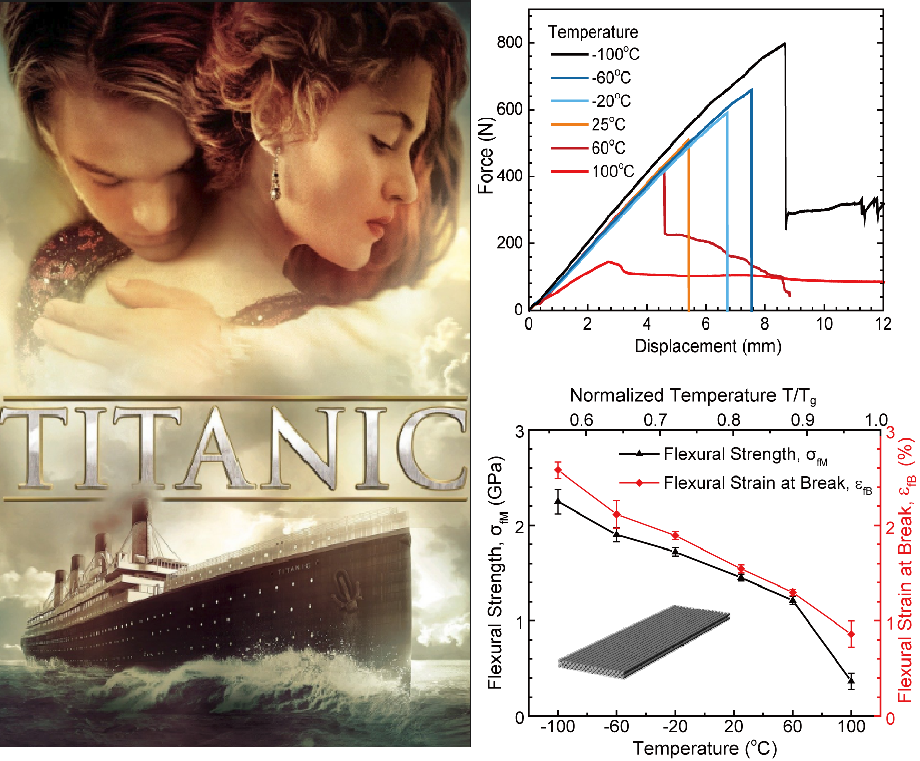
Similar to steel, the mechanical properties of the polymer matrix are also highly temperature dependent: as temperature decreases, it becomes brittle and cracks can propagate easily. Therefore, the mechanical responses of carbon fiber reinforced polymers (CFRP) at extreme temperature conditions need to be studied carefully such that using them at unfavorable temperatures could be avoided.
Carbon fiber reinforced polymer composites are increasingly used in civil, naval, aerospace, and wind energy applications, where they can be frequently exposed to harsh temperature conditions and under static and dynamic loads. In the literature, however, the reports on the temperature effect is inconsistent. While some studies report that CFRP becomes stronger at lower temperatures while others show the opposite trend.
Our study conclude that CFRP becomes stiffer, stronger, and tougher at lower temperatures.
To have a convincing conclusion on how temperature affects the mechanics of CFRP and reveal the underlying mechanics. We experimentally investigates the effect of temperature, ranging from -100 °C to 100 °C, under static and dynamic three-point bending tests. Our results clearly demonstrate that CFRPs exhibit enhanced flexural strength, maximum deflection, and energy absorption at lower temperatures (-60 °C, -100 °C) while relatively poor behaviors at higher temperature (100 °C).
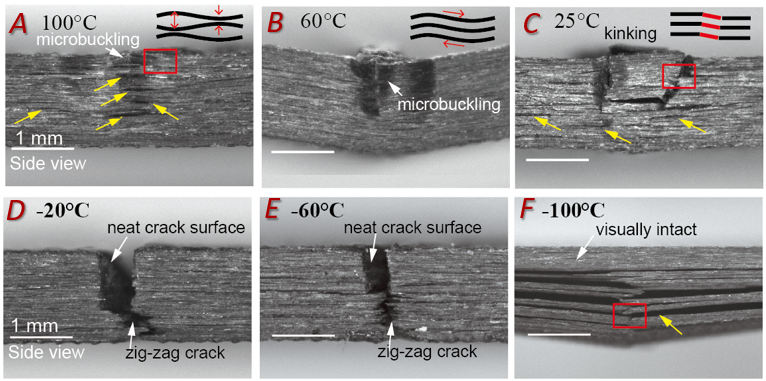
Experimental images from post-mortem photographs, scanning electron microscopy, and high speed videos are implemented to observe various failure behaviors including microbuckling, kinking, and fiber breakage at different temperatures. Simple analytical models are proposed to explain the experimental observation. In short, the underlying toughening mechanism can be understand as "a stiffer matrix makes fiber reinforced composites stronger and tougher".
A stiffer matrix makes the fiber reinforced composites stronger and tougher.

A more precise description of the underlying toughening mechanisms is: 1) improved critical stress of microbuckling, kinking, and ultimate tensile stress at lower temperatures, 2) a failure mode transition from upper layer microbuckling to bottom layer tensile breakage, and 3) forming extensive microcracks when the temperature is extremely low. These mechanisms come from the “brittle” nature of the polymer matrix at lower temperatures – higher Young’s modulus and smaller ultimate tensile strain.

The effect of increasing strain rate is found similar to temperature decreasing (time temperature equivalence principle), which improves the mechanical property of the composite. Importantly, the finding reported here offers pathways to improve the structure integrity design by taking advantage of the favorable damage patterns and avoiding the unfavorable ones.
Interested reader may refer to my poster and our paper published in Composites Science and Technology for more details.
Comments